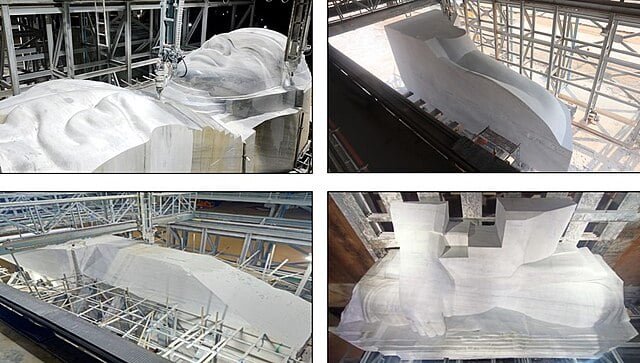
Imagine this: a raw, cold, and rigid block of aluminum rests on a metal altar. Suddenly, a robotic arm descends, its metallic fingers gripping a diamond-tipped scalpel. With a buzzing symphony, the metal surrenders, carved into intricate gears, delicate curves, and incredibly precise shapes. This, my friends, is the magic of CNC machining.
Manufacturing industries are constantly pressured by market demands to produce high-quality, cost-effective products (Imad et al., 2022). To cope with this, companies must embrace advanced manufacturing technologies that are efficient and highly accurate.
CNC machining is a revolutionary technology redefining the industry. With its ability to automate and optimize complex manufacturing processes, CNC machining offers unparalleled precision and consistency.
With CNC machining, manufacturers can tackle more complex projects and deliver exceptional products that meet the strictest specifications. From aerospace components to medical devices, CNC machining is the ideal solution for industries where precision is non-negotiable.
The global market for CNC machines was estimated at US $95 billion in 2022 and is projected to reach US $154 billion by 2032, representing an annual growth rate of 5% over the same period.
In this article, we will explore the various applications of CNC machining and the benefits it brings to precision manufacturing. Let’s delve into the world of precision and discover how CNC machining is transforming the industry.
What is CNC Machining?
CNC machining, or Computer Numerical Control machining, is a manufacturing process that uses a computer to control the movement of a cutting tool. The cutting tool removes material from a block of material, such as metal, plastic, or wood, to create a piece with the desired shape and size.
Computer Numerical Control machining, also known as CNC Machining, is a subtractive manufacturing process. This process is used to create a wide range of parts, from simple prototypes to complex components for the aerospace industry.
Using advanced computer software, CNC machines can perform complex tasks with minimal human intervention. This not only eliminates the risk of human error but also increases productivity and reduces costs.
By harnessing the power of CNC machining, manufacturers can achieve greater efficiency, shorter delivery times, and improved product quality. As technology continues to evolve, the possibilities of CNC machining are limitless, opening new opportunities for businesses to thrive in an increasingly competitive landscape.
Advantages of CNC Machining
In the last decade, many factories have been replacing their industrial machinery with Computer Numerical Control (CNC) machines because they are more durable, robust, and cost-effective for precision component manufacturing operations (Kumar et al., 2016).
CNC machining brings numerous advantages:
- Eliminates the risk of human error: Traditional manufacturing methods are prone to errors made by human operators, compromising the quality of the final product. CNC machines, on the other hand, follow precise instructions programmed into their software, ensuring consistent and accurate results.
- Significantly increases productivity: With the ability to operate continuously, 24 hours a day, seven days a week, CNC machines can produce parts at a much faster rate compared to manual labor. This not only reduces delivery times but also allows manufacturers to take on larger work volumes.
- Long-term cost savings: While the initial investment in CNC machines may be higher compared to traditional equipment, the reduced need for labor and avoidance of costly errors ultimately lead to lower production costs. Manufacturers can also optimize material usage using the precision of CNC machines, minimizing waste and saving money.
Common Applications of CNC Machining
CNC machining finds applications in a wide range of industries and products.
- In aerospace manufacturing, CNC machines play a crucial role in producing complex components such as turbine blades and structural parts. The precision and consistency of CNC machining ensure that these critical components meet the stringent requirements of the aerospace industry.
- The medical field also greatly benefits from CNC machining. From surgical instruments to prosthetics, CNC machines are used to create complex and custom medical devices. The high level of precision achieved through CNC machining ensures that these devices fit perfectly and function seamlessly, improving patient outcomes.
- Automotive manufacturing is another industry where CNC machining is widely used. From engine components to body panels, CNC machines enable the production of high-quality parts that meet the demanding standards of the automotive industry. CNC machining also facilitates rapid prototyping and iterative design, speeding up the development process and bringing new vehicles to market more quickly.
How CNC Machining Works
Essentially, CNC machining relies on computer numerical control. This means the machine operates according to a set of pre-programmed instructions. These instructions are created using computer-aided design (CAD) software, allowing engineers to design complex parts with precise dimensions.
Once the design is complete, the CAD file is converted into a format that the CNC machine can understand. This is typically done using computer-aided manufacturing (CAM) software. The CAM software generates a set of instructions, known as G-code, instructing the CNC machine on how to move and operate its tools.
Next, the CNC machine executes the G-code, performing the necessary cuts, drills, and carvings to create the final piece. The machine’s movements are controlled by servos, which are motors that precisely position the cutting tools. The result is a piece that precisely matches the specifications described in the CAD file.
Types of CNC Machines
CNC machining encompasses various machine types, each suitable for different manufacturing needs. The most common ones are milling and turning machines.
- CNC Milling: A common type is the CNC milling machine, which uses rotating cutting tools to remove material from a workpiece. CNC milling machines are versatile and can be used to create simple tasks, as well as both simple and complex parts.
- CNC Turning: Lathes rotate the workpiece while a stationary cutting tool shapes it as desired. CNC lathes are commonly used for cylindrical parts, such as shafts and bushings.
There are also specialized CNC machines, such as CNC routers for woodwork and CNC plasma cutters for metal fabrication. These machines cater to specific industries and have unique features tailored to their respective applications.
How to Choose the Right CNC Machine?
Selecting the right CNC machine for your manufacturing needs is crucial to maximize efficiency and quality. Factors to consider include the type of parts you will produce, the materials you will work with, and the desired level of automation.
For small-scale production or prototyping, a compact CNC machine may be suitable. These machines are often more affordable and can operate in a smaller workspace. However, they may have limitations in terms of size and capabilities.
For larger-scale production, a high-speed CNC machine with multiple axes may be necessary. These machines can handle complex parts and offer faster cycle times, increasing productivity. They are often equipped with automatic tool changers, allowing uninterrupted operation.
It’s also important to consider the support and training provided by the CNC machine manufacturer. Proper training ensures operators can fully utilize the machine’s capabilities and troubleshoot any issues that may arise.
Tips for Maximizing Efficiency in CNC Machining
To maximize efficiency in Computer Numerical Control machining, several tips should be considered. Firstly, optimizing toolpaths can significantly reduce machining time. By minimizing unnecessary movements and strategically making cuts, manufacturers can decrease cycle times and increase productivity.
Secondly, proper tool selection is crucial. Using the right tools for the job ensures optimal cutting performance and extends tool life. Manufacturers should consider factors such as material hardness, cutting speed, and feed rate when selecting tools.
Additionally, regularly maintaining and calibrating CNC machines is essential for consistent performance. This includes cleaning the machine, lubricating moving parts, and checking for signs of wear or damage. Regular maintenance not only improves machine longevity but also ensures precise and reliable machining.
Importance of Quality Control in CNC Machining
While Computer Numerical Control machining offers unparalleled precision, quality control remains a critical aspect of the process. Manufacturers must implement robust quality control measures to ensure that each piece meets the required specifications.
This includes conducting periodic inspections during and after machining to verify dimensional accuracy, surface finish, and any defects. Advanced metrology equipment, such as Coordinate Measuring Machines (CMM), can be used to check the dimensions of critical elements with high precision.
In addition to dimensional accuracy, quality control also encompasses testing and material certification. Manufacturers must ensure that the raw materials used in Computer Numerical Control machining meet the required standards and have the necessary certifications. This ensures the integrity and performance of the final product.
How to Find a CNC Machining Shop?
Finding the right CNC machining shop is crucial for the success of your project. Here is a guide on how to do it:
- Define your requirements: Clearly describe your project requirements, including materials, tolerances, and quantities. This will help narrow down the list of suitable CNC machine shops.
- Search and shortlist: Use online platforms, directories, and recommendations to identify potential CNC machine shops. Look for shops with experience in your industry and a track record of similar projects.
- Evaluate capabilities: Assess the shop’s capabilities in terms of equipment, technology, and experience. Ensure they have the right CNC machines for your specific needs.
- Check Certifications and Quality Standards: Verify if the CNC machining shop has relevant certifications and complies with quality standards. This ensures their processes meet industry requirements.
- Reviews and references: Read customer reviews and ask for references. Feedback from previous customers can provide insights into the reliability, communication, and quality of the shop’s work.
- Prices and Quotes: Request quotes from multiple CNC machine shops. While cost is a factor, overall value, including quality, delivery times, and customer service, should also be considered.
- Communication: Evaluate the communication style of potential providers. A Computer Numerical Control machining shop that responds and communicates effectively is more likely to address any concerns or changes during the project.
- Delivery Timelines: Analyze project timelines and ensure the CNC machining shop can meet your deadlines. Delays can have a significant impact on the overall project schedule.
- Visit Facilities: If possible, visit the CNC machine shop to assess its facilities, meet the team, and see its operations firsthand.
- Patents and Contracts: If your project involves proprietary information, ensure the CNC machining shop is willing to sign a Non-Disclosure Agreement (NDA). Clearly define project details, responsibilities, and expectations in a contract.
- Start with a Small Project: Consider starting with a smaller project to assess the performance of the CNC machining shop before committing to larger and more complex work.
- Regular Updates: Establish a communication plan and expect regular updates on the progress of your project. This ensures transparency and allows for timely adjustments if needed.
Remember, choosing the right Computer Numerical Control machining shop is a crucial step in the manufacturing process. Take your time, thoroughly research, and prioritize a shop that aligns with your project requirements and business goals.
CNC Machining Directories
Finding a suitable CNC machining shop can be crucial for your project’s success. Here is a list of popular online directories where you can search for CNC machining services:
- ThomasNet is an extensive industrial directory that includes a wide range of manufacturing services, including CNC machining.
- MFG connects buyers with manufacturers, and you can find CNC machining services by specifying your requirements.
- CNCPros is a directory specifically focused on CNC machining services. You can search for shops based on their location, capabilities, and materials.
- Xometry is an online marketplace that connects businesses with various manufacturing services, including CNC machining.
- MFG Center is a comprehensive directory covering diverse manufacturing services, including CNC machining.
- CNC Machining Zone is a directory specifically focused on CNC machining services, making it easy to find relevant shops.
- CNC Machining Search Engine: This search engine allows you to find CNC machining shops based on location and specific machining capabilities.
- IndustryNet is an industrial marketplace that includes a wide range of manufacturing services, including CNC machining.
When using these directories, be sure to input your specific requirements to effectively narrow down your search. Additionally, always check reviews, certifications, and capabilities to ensure that a CNC machining shop aligns with your project needs.
The Future of CNC Machining
As technology continues to evolve, the future of CNC machining looks promising. Advances in artificial intelligence and machine learning are making CNC machines even smarter and more autonomous. These machines can adapt to changing conditions, optimize tool paths in real-time, and detect potential errors before they occur.
According to Ntemi et al., (2022), “the Industry 4.0 revolution drives the integration of advanced control technologies by incorporating artificial intelligence and machine learning, leading to the development of intelligent CNC machining systems”; similarly, von Hahn and Mechefske (2022) developed a machine learning system that can be used in CNC machining.
Furthermore, the integration of additive manufacturing, or 3D printing, with CNC machining opens new possibilities. This combination allows for the creation of complex geometries and the production of parts with different material properties. The ability to add material layer by layer offers unprecedented design freedom and manufacturing flexibility.
Key Trends in CNC Machining
The world of CNC machining is constantly filled with innovation and exciting new trends. Here are some trends:
- Micro-machining
The demand for increasingly smaller and precise components is driving the micro-machining revolution. Think about complex parts for medical implants, microfluidics, and next-generation electronics. These tiny titans are pushing the boundaries of what’s possible and require specialized machines and ultra-thin cutting tools.
- Sustainability takes center stage
Eco-friendly CNC machining is no longer just a niche trend; it is becoming the new standard. From energy-efficient machines and recyclable materials to reducing waste generation, sustainability is at the forefront of discussions. Companies are seeking ways to minimize their environmental impact while maintaining their competitive advantage.
- The rise of collaborative robots
Collaborative robots, or cobots, are transforming the CNC landscape. These friendly robots work alongside human machinists, automating repetitive tasks and improving safety. This human-robot duo is boosting productivity, enhancing ergonomics, and opening doors for workers with disabilities.
- Machining the “unmachinable”
Pushing the limits of materials, researchers are exploring the machinability of exotic materials such as ceramics, superalloys, and even biomaterials. This opens doors to cutting-edge applications in the aerospace sector, medical devices, and more.
With these advancements, CNC machining is poised to further revolutionize precision manufacturing. The industry can expect increased efficiency, shorter delivery times, and better product quality as CNC machines continue to push the limits of what’s possible.
Conclusion
In conclusion, CNC machining is revolutionizing precision manufacturing by maximizing efficiency and quality. With its ability to automate and optimize complex processes, CNC machining offers unparalleled precision, consistency, and productivity.
From aerospace components to medical devices, CNC machining finds applications in various industries where precision is non-negotiable. The advantages of CNC machining, such as eliminating human errors, increasing productivity, and reducing costs, make it the ideal solution for manufacturers seeking superior results.
The future of CNC machining looks bright. With the integration of AI, machine learning, and additive manufacturing, CNC machines are becoming even smarter, more autonomous, and capable of producing complex parts with ease.
However, it’s crucial to remember that quality control remains crucial in CNC machining. Solid quality control measures ensure that each piece meets the required specifications, providing customers with exceptional products they can trust.
In the ever-evolving landscape of precision manufacturing, CNC machining is redefining the industry, pushing the boundaries of what’s possible, and enabling businesses to thrive in a competitive market. With its ability to maximize efficiency and quality, CNC machining is truly transforming precision manufacturing.
References
Imad M., C. Hopkins, A. Hosseini, N.Z. Yussefian & H.A. Kishawy (2022) Intelligent machining: a review of trends, achievements and current progress, International Journal of Computer Integrated Manufacturing, 35:4-5, 359-387, DOI: 10.1080/0951192X.2021.1891573
Kumar, R. S., Thangarasu, V. S., & Alexis, S. J. (2016). Adaptive control systems in CNC machining processes–a review. Advances in Natural and Applied Sciences, 10(6 SE), 120-130.
Ntemi, M., Paraschos, S., Karakostas, A., Gialampoukidis, I., Vrochidis, S., & Kompatsiaris, I. (2022). Infrastructure monitoring and quality diagnosis in CNC machining: A review. CIRP Journal of Manufacturing Science and Technology, 38, 631-649.
von Hahn, Tim, and Chris K. Mechefske. 2022. “Machine Learning in CNC Machining: Best Practices” Machines 10, no. 12: 1233. https://doi.org/10.3390/machines10121233