In the current rapidly evolving business landscape, organizations strive to achieve excellence in product development and process improvement to maintain a competitive edge. A methodology that has emerged as a model of success in this quest is Design for Six Sigma (DFSS).
Design for Six Sigma has the power to optimize processes, eliminate defects, and drive innovation. Developing new products in the shortest possible time, with competitive pricing, quality, and addressing the dynamics of the consumer market and economic fluctuations has been a major challenge for the business world (Francisco et al., 2020).
Product design and development are part of the daily life of every company; in this sense, when a new product is introduced or reintroduced, Design for Six Sigma can be employed in the process (Jenab and Moslehpour, 2018). Thus, the DFSS methodology constitutes an important tool for entrepreneurs.
In this guide, we want to delve into the principles, methodologies, tools, and benefits of Design for Six Sigma, enabling you to achieve innovative results in product development and business performance.
What is Design for Six Sigma (DFSS)?
Design for Six Sigma (DFSS) is a structured methodology that integrates the principles of Six Sigma with design thinking to prevent defects from occurring from the outset. It is a proactive approach that focuses on designing new products, processes, and services that are virtually error-free from the start.
Design for Six Sigma is primarily used to create or completely redesign a product or process. Carvalho et al. (2016) highlight that DFSS requires applying resources to discover what customers want and then dedicating the entire project to meeting the needs and desires of these customers.
Six Sigma and Design for Six Sigma
Design for Six Sigma is a proactive approach to product and process design that aims to minimize defects and variations while maximizing customer satisfaction. Unlike traditional Six Sigma methodologies that focus on improving existing processes, DFSS is applied during the design phase to ensure that products and processes meet customer requirements from the outset. In this regard, Haktanır and Kahraman (2021) emphasize that in Design for Six Sigma (DFSS), the aim is to minimize variation by applying the techniques of the Six Sigma approach.
Origins and Evolution of DFSS
DFSS emerged in the 1990s as an extension of Six Sigma, which was originally developed by Motorola in the 1980s to improve manufacturing processes. DFSS recognized that preventing defects in the early stages of the design phase was much more cost-effective and efficient than fixing them later in the production cycle.
Key Principles of Design for Six Sigma (DFSS)
The basic principles of DFSS are:
- Customer Focus: Understanding and prioritizing customer needs throughout the design process.
- Prevention over Inspection: Preventing defects from occurring rather than relying on inspection to detect them.
- Design for Quality: Incorporating quality principles into the design process from the outset.
- Data-Driven Decision Making: Using data to inform design decisions and measure progress.
- Teamwork and Collaboration: Fostering a collaborative environment where diverse perspectives are valued.
- Continuous Improvement: DFSS fosters a culture of continuous improvement, where lessons learned from each project inform future iterations and innovations.
Unveiling the Methodologies for Design for Six Sigma
In the scientific literature, you can find different methodologies for implementing DFSS; however, Francisco et al., (2020) highlights that the main ones are DMADV (define, measure, analyze, design, and verify) and IDOV (identify, design, optimize, and validate).
DMADV: The define, measure, analyze, design, and verify cycle
DMADV is a design methodology used to create new products, processes, or services, this methodology is similar to the DMAIC method (define, measure, analyze, improve, and control) used in Six Sigma. Wang et al., (2016) emphasizes that to meet and satisfy customer requirements, the DMADV framework is the most effective approach that can be used to ensure that products meet specifications.
The DMADV cycle involves the following steps:
- Define: Clearly define your customer’s needs and project objectives. According to Carvalho et al., (2016), this phase consists of identifying the product, service, or process to be built (or rebuilt).
- Measure: Collect information about your customers’ needs, market trends, and competitive landscape. This information should be converted into measurable (measurable) characteristics.
- Analyze: Analyze the data from the previous phase to identify opportunities and limitations. Develop an action plan to meet customer quality requirements.
- Design: Develop and evaluate alternative design solutions. Customer quality requirements become critical elements of the process. This is one of the critical steps in the entire process. As an example, Krulčić et al., (2023) apply Design for Six Sigma (DFSS) principles to analyze different scenarios using digital twin models for simulation and determine the best configuration for the manufacturing system.
- Verify: Test and validate the chosen design to ensure it meets requirements.
Harnessing the Power of DFSS Tools
Design for Six Sigma offers a wide range of tools to support its methodologies. These tools can be classified into the following areas:
DFSS Tools for Defining Project Scope
- Voice of the Customer (VOC): Capturing and analyzing customer needs and expectations.
- Quality Function Deployment (QFD): Translating customer needs into technical requirements.
- Theory of Inventive Problem Solving (TRIZ): TRIZ is a methodology for solving inventive problems and can aid in companies’ innovation processes. Want et al., (2016) reports that DFSS with TRIZ can serve as a mechanism to revolutionize the way companies develop new products.
- Project Charter: Defining project objectives, scope, and deliverables.
DFSS Tools for Measuring and Analyzing Processes
- Process Mapping: Creating a visual representation of a process to identify inefficiencies and bottlenecks.
- Data Collection Methods: Gathering quantitative and qualitative data to understand process performance.
- Statistical Analysis: Using statistical techniques to identify trends, correlations, and root causes.
DFSS Tools for Improving and Designing Processes
- Brainstorming: Generating creative ideas for process improvement or design.
- Design of Experiments (DOE): Testing the effects of different factors on process outcomes.
- Failure Mode and Effects Analysis (FMEA): Identifying and prioritizing potential failure modes.
DFSS Tools for Controlling and Sustaining Improvements
- Control Charts: Monitoring process performance and identifying deviations from standard.
- Standard Operating Procedures (SOP): Documenting and standardizing best practices.
- Error Proofing: Implementing measures to prevent human errors.
Discovering the Tangible Benefits of Design for Six Sigma
The implementation of Design for Six Sigma has yielded significant benefits for organizations across various industries. These benefits include:
Join the Community
Get the best ideas, analysis, and trends on innovation delivered straight to your inbox. No spam, just value!
Improving customer satisfaction and product quality
- Reducing defects and enhancing product reliability.
- Increased customer satisfaction and loyalty.
- Strengthened brand reputation.
Reducing costs and improving efficiency
- Minimized waste and rework.
- Optimized processes and reduced cycle times.
- Lower production costs and increased profitability.
Gaining a competitive edge through innovation
- Accelerated product development and time-to-market.
- Introduction of innovative products and services.
- Enhanced competitive advantage and market share.
Case Studies of Successful DFSS Implementations
Numerous organizations have successfully implemented Design for Six Sigma and achieved remarkable results. Examples include:
- Information Technology Solution: Mitchell and Kovach (2016) used the DFSS methodology to design an information technology solution that effectively communicates information between layers within the supply chain regarding the movement of materials through inland barge tankers; the experience led to improved communication and decision-making within the supply chain.
- Construction Sector: Lee et al., (2020) propose the use of an advanced composite material-based concrete formwork for workers using a Design for Six Sigma (DFSS) process to improve the constructability of the formwork system; and the study demonstrated how DFSS will be a valuable tool for technological development and systematic decision-making in building construction.
- Food Processor: Decesari et al., (2020) applied the Design for Six Sigma (DFSS) methodology to the design of an innovative food processor, and it has been implemented through Creo Parametric software.
- Additive Manufacturing: Sithole et al., (2021) evaluated the applicability of Six Sigma design principles to Additive Manufacturing, and determined the importance of applying the DFSS methodology because additive manufacturing requires process design optimization every time a new product is manufactured.
- Reduction of Environmental Pollution: Donnici et al., (2022) developed the “Buttalo” service to encourage the population to fight environmental pollution and, at the same time, helping smokers become aware of it by properly disposing of cigarette “butts”; they employed appropriate product design methods such as TRIZ and QFD driven by DFSS, to conceive new products and services to create incentives for smokers to decrease the environmental pollution problem.
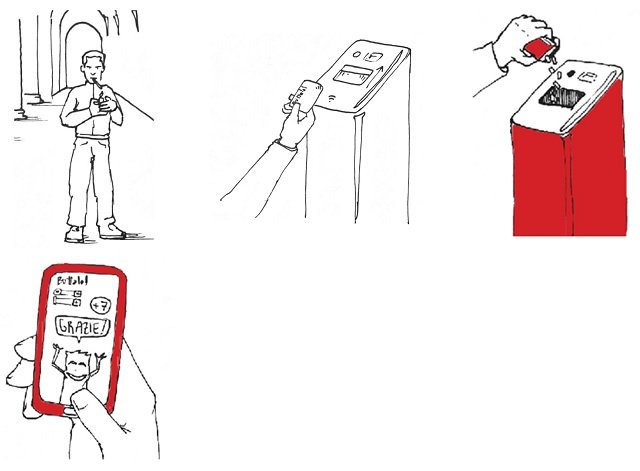
These case studies demonstrate the power of DFSS to drive innovation and continuous improvement.
DFSS Implementation: A Roadmap to Success
Successful implementation of Design for Six Sigma requires a structured approach and leadership commitment. If your goal is to develop a new product, Francisco et al., (2020) and Francisco et al., (2023) propose a roadmap for using Design for Six Sigma in the product development process; while Yang et al., (2022) developed a new DFSS process as Define, Identify, Measure, Design, Optimize, and Verify (DIMDOV).
In summary, key aspects for implementing Design for Six Sigma include:
Establishing a DFSS Culture within the Organization
- Create a supportive environment that values quality and continuous improvement.
- Integrate DFSS principles into the organization’s culture and values.
- Provide training and education to all employees on DFSS concepts and tools.
Selection and Training of Design for Six Sigma Leaders
- Identify individuals dedicated to leading and promoting DFSS initiatives.
- Provide comprehensive training to DFSS champions on methodology and tools.
- Empower DFSS champions to facilitate project implementation and train others.
Effective DFSS Project Management
- Establish clear project goals, objectives, and scope.
- Use appropriate project management methodologies.
- Ensure effective communication and collaboration among team members.
Overcoming Common Design for Six Sigma Implementation Challenges
- Obtain executive buy-in and secure resources.
- Change organizational culture and overcome resistance to change.
- Integrate DFSS with existing processes and systems.
- Maintain long-term commitment to continuous improvement.
Key Strategies for Successful Implementation
While DFSS offers immense potential for driving innovation and quality, successful implementation requires careful planning and execution. Some key strategies to ensure success include:
- Executive Sponsorship: Securing executive sponsorship and leadership buy-in is critical to gaining organizational support and resources for DFSS initiatives.
- Cross-Functional Teams: Since Design for Six Sigma projects often involve multiple departments and disciplines, forming cross-functional teams ensures that diverse perspectives and expertise are effectively leveraged.
- Continuous Monitoring and Adaptation: Continuous monitoring of project progress and results allows teams to identify and address issues in real-time, ensuring timely course corrections and optimization.
- Celebration of Success: Recognizing and celebrating project milestones and successes fosters a culture of achievement and motivates teams to maintain momentum and drive continuous improvement.
Conclusion: Embracing DFSS for Innovation and Continuous Improvement
Design for Six Sigma continues to evolve and adapt to meet the ever-changing needs of organizations. As technology advances and customer expectations increase, DFSS will remain an essential tool for driving continuous improvement and innovation.
DFSS is not a one-time project but a continuous journey of continuous improvement. Organizations that embrace Design for Six Sigma as a culture and mindset will reap long-term benefits in terms of quality, efficiency, and innovation.
By effectively implementing Design for Six Sigma, organizations can unlock their true potential, achieve sustainable growth, and gain a competitive edge in the market. DFSS is a powerful tool that can transform organizations and propel them towards excellence.
Bibliographical References
Carvalho, M.S., Magalhaes, D.s., Varela, M.L., Sa, J.O. and Gonçalves, I. (2016), “Definition of a collaborative working model to the logistics area using design for Six Sigma“, International Journal of Quality & Reliability Management, Vol. 33 No. 4, pp. 465-475. https://doi.org/10.1108/IJQRM-11-2014-0190
Decesari, C., Frizziero, L., & Liverani, A. (2020). Design For Six Sigma Applied to the Design of an Innovative Food Processor. In PROCEEDINGS INTERNATIONAL CONFERENCE ON INDUSTRIAL ENGINEERING AND OPERATIONS MANAGEMENT (No. August, pp. 1868-1888). IEOM Society.
Donnici, G., Frizziero, L., & Liverani, A. (2022). Design for Six Sigma and TRIZ for Inventive Design Applied to Recycle Cigarette Butts. Designs, 6(6), 122. https://doi.org/10.3390/designs6060122
Francisco, M.G., Canciglieri Junior, O. and Sant’Anna, Â.M.O. (2020), “Design for six sigma integrated product development reference model through systematic review“, International Journal of Lean Six Sigma, Vol. 11 No. 4, pp. 767-795. https://doi.org/10.1108/IJLSS-05-2019-0052
Francisco, M.G., Canciglieri Junior, O. and Santanna, A.M.O. (2023), “Roadmap for product development based on design for six sigma method“, International Journal of Lean Six Sigma, Vol. 14 No. 5, pp. 989-1009. https://doi.org/10.1108/IJLSS-06-2022-0131
Haktanır, E., Kahraman, C. (2021). Design for Six Sigma and Process Capability Using Penthagorean Fuzzy Sets. In: Kahraman, C., Cevik Onar, S., Oztaysi, B., Sari, I., Cebi, S., Tolga, A. (eds) Intelligent and Fuzzy Techniques: Smart and Innovative Solutions. INFUS 2020. Advances in Intelligent Systems and Computing, vol 1197. Springer, Cham. https://doi.org/10.1007/978-3-030-51156-2_161
Jenab, K., Wu, C & Moslehpour, S. (2018). Design for six sigma: A review Management Science Letters , 8(1), 1-18.
Krulčić, E., Doboviček, S., Matika, D., & Pavletić, D. (2023). Design for Six Sigma Digital Model for Manufacturing Process Design. Tehnički glasnik, 17(2), 215-222.
Lee, D. ., Kim, T. ., Lee, D. ., Lim, H. ., Cho, H. ., & Kang, K.-I. . (2020). Development of an advanced composite system form for constructability improvement through a Design for Six Sigma process. Journal of Civil Engineering and Management, 26(4), 364-379. https://doi.org/10.3846/jcem.2020.12188
Mitchell, E. M., & Kovach, J. V. (2016). Improving supply chain information sharing using Design for Six Sigma. European Research on Management and Business Economics, 22(3), 147-154. https://doi.org/10.1016/j.iedee.2015.02.002
Sithole, C., Gibson, I., & Hoekstra, S. (2021). Evaluation of the applicability of design for six sigma to metal additive manufacturing technology. Procedia CIRP, 100, 798-803. https://doi.org/10.1016/j.procir.2021.05.041
Wang, F., Yeh, C., & Chu, T. (2016). Using the design for Six Sigma approach with TRIZ for new product development. Computers & Industrial Engineering, 98, 522-530. https://doi.org/10.1016/j.cie.2016.06.014
Yang, C., Jou, Y., Lin, M., Silitonga, R. M., & Sukwadi, R. (2022). The Development of the New Process of Design for Six Sigma (DFSS) and Its Application. Sustainability, 14(15), 9294. https://doi.org/10.3390/su14159294

Editor and founder of “Innovar o Morir” (‘Innovate or Die’). Milthon holds a Master’s degree in Science and Innovation Management from the Polytechnic University of Valencia, with postgraduate diplomas in Business Innovation (UPV) and Market-Oriented Innovation Management (UPCH-Universitat Leipzig). He has practical experience in innovation management, having led the Fisheries Innovation Unit of the National Program for Innovation in Fisheries and Aquaculture (PNIPA) and worked as a consultant on open innovation diagnostics and technology watch. He firmly believes in the power of innovation and creativity as drivers of change and development.