Imagine a factory where machines communicate with each other, robots work alongside humans, and production is optimized in real-time. This is the vision of Industry 4.0, the fourth industrial revolution that is transforming the manufacturing sector.
Industry 4.0, also known as the Fourth Industrial Revolution, is revolutionizing the way companies manufacture, improve, and distribute their products and services through technologies such as artificial intelligence, the Internet of Things, and robotics; in this sense, it is creating a new competitive environment.
The concepts and technologies of Industry 4.0 can be applied to all types of industrial companies and sectors, and it is not just about investing in new technology and tools to improve manufacturing efficiency, it is about revolutionizing the way your business works and grows.
Several specialists recognize that Industry 4.0 represents a great opportunity to develop and improve competitiveness, although the state of readiness for its implementation varies widely depending on the country, sector, or individual companies (Ślusarczyk, 2018). In this sense, if you are leading a company, you must start preparing your organization to start the path toward intelligent manufacturing.
In this article, we present information about the definition, characteristics, technologies, and examples of Industry 4.0, and also how it differs from Industry 5.0.
What is Industry 4.0?
The term Industry 4.0, also known as the Fourth Industrial Revolution, was introduced at the Hannover Messe in 2011 (Giallanza et al., 2020), and the German government launched Industry 4.0 as a high-tech plan for German industries in 2014 (Gonçalves et al. 2020; Xu et al., 2021).
Synonymous with smart manufacturing, Industry 4.0 is the realization of the digital transformation of the field, which allows for real-time decision-making, greater productivity, flexibility, and agility (IBM, ?).
Gonçalves et al., (2020) point out that “the concept of Industry 4.0 is associated with the technical perspective of a Cyber-Physical System (CPS) integrated into manufacturing operations and with Internet of Things (IoT) technologies in industrial processes, which can be represented by smart factories, smart products, and extended value networks: vertical, horizontal and end-to-end integration”.
In this sense, we can define Industry 4.0 as the transformation of the manufacturing industry through the adoption of advanced technologies such as artificial intelligence (AI), the Internet of Things (IoT), robotics, 3D printing, among others. This new era of manufacturing is characterized by connectivity, automation, machine learning, and the digitization of production processes.

Characteristics of Industry 4.0
Industry 4.0 is the fourth industrial revolution in human history. The first industrial revolution, which took place in the 18th century, was marked by the introduction of the steam engine and the mechanization of production. The second industrial revolution, in the late 19th and early 20th centuries, was characterized by mass production and the use of electricity. The third industrial revolution, which began in the 1970s, was driven by automation and electronics.
The Fourth Industrial Revolution is characterized by the convergence of physical and digital spaces, which is revolutionizing the way production operations are managed (Guo et al., 2021).
Manufacturers are integrating new technologies, including the Internet of Things (IoT), cloud computing and analytics, artificial intelligence (AI), and machine learning into their production facilities and throughout their operations. In this regard, Meindl et al (2021) describes four dimensions of Industry 4.0: smart manufacturing, smart products and services, smart supply chain, and smart work.
In this way, smart manufacturing is characterized by the increase in automation and the use of intelligent machines and smart factories, informed data helps to produce goods more efficiently and productively across the value chain.
Marr (2018) highlights that connected machines collect a tremendous volume of data that can inform maintenance, performance, and other issues, as well as analyze the data to identify patterns and signals that may be impossible for humans to perform in a reasonable amount of time.
For their part, Agrawal et al (2020) describe that the fourth industrial revolution is characterized by 4 foundational technologies applied throughout the value chain:
- Connectivity, data, and computing power: sensors, internet of things, cloud technology, and blockchain.
- Analytics and intelligence: advanced analytics, machine learning, and artificial intelligence.
- Human-machine interaction: virtual and augmented reality, robotics and automation, chatbots.
- Advanced engineering: additive manufacturing, renewable energy, and nanoparticles.
Benefits of Industry 4.0
Industry 4.0 offers many benefits for manufacturing companies, including:
- Increased efficiency and productivity: The automation and digitization of production processes can help companies reduce production time, increase efficiency, and improve productivity.
- Reduced costs: Industry 4.0 can help companies reduce production, labor, and maintenance costs.
- Improved product quality: AI and IoT can help companies improve product quality by detecting defects early and optimizing production processes.
- Increased flexibility and customization: Industry 4.0 allows companies to be more flexible and agile to adapt to changing market demands.
- New business models: Industry 4.0 opens the door to new business models, such as on-demand manufacturing and pay-per-use services.
Impact of Industry 4.0 on manufacturing
Industry 4.0 is having a significant impact on the manufacturing industry, transforming the way products are designed, produced, and managed. Some of the most important changes include:
- Digital transformation of the supply chain: Industry 4.0 is driving the digitization of the supply chain, enabling greater visibility and control of material and information flows.
- Automation and robotics: Automation and robotics are playing an increasingly important role in manufacturing, leading to a reduction in labor and an increase in productivity.
- Smart and connected manufacturing: Smart and connected factories use sensors and the IoT to collect real-time data on production processes, enabling smarter decision-making and improved efficiency.
- Implications for the workforce: Industry 4.0 is creating new professional opportunities for people who have developed skills in digital technologies; however, it will also harm people who do not perform specialized tasks.
For consumers, Industry 4.0 can lead to:
Join the Community
Get the best ideas, analysis, and trends on innovation delivered straight to your inbox. No spam, just value!
- Lower prices
- Higher quality products
- Greater diversity of products to choose from
- More personalized and sustainable products
Likewise, Ching et al., (2022) report that the different sustainability functions of Industry 4.0 contribute to the development of the economic, environmental, and social dimensions of sustainability.
Advantages and disadvantages of Industry 4.0
The Fourth Industrial Revolution offers many advantages for entrepreneurs because it allows many processes to be automated, but perhaps the main advantage is having information in real-time that can facilitate decision-making.
According to IBM, the use of high-tech Internet of Things devices in smart factories leads to increased productivity and better quality.
Industry 4.0 provides new features and possibilities in manufacturing in two main aspects: the added value to the final customer and the capabilities of the production process (Oláh et al., 2020).
Masood et al (2020) in their study with small and medium-sized companies in the United Kingdom found that flexibility, costs, efficiency, quality, and competitive advantage are the key benefits of adopting Industry 4.0.
Despite the advantages, Industry 4.0 has some disadvantages; among the main ones are that since all equipment and software are interconnected, a cyberattack could affect the entire company.
On the other hand, the investment required to implement the technology in many countries still has a high cost, which is a disadvantage for many micro and small businesses.
What technologies are driving Industry 4.0?
The Fourth Industrial Revolution is mainly characterized by the intensive use of information and communication technologies in all processes and the value chain.
According to the reports by IBM (?), Oláh et al., (2020) and Sigov et al (2022) the following technologies are the ones that are driving the Fourth Industrial Revolution:
- Internet of Things (IoT)
- Cloud Computing
- Artificial Intelligence (AI) and Machine Learning
- Edge Computing
- Cybersecurity
- Digital Twin
- Big Data Analytics
- 3D Printing
- Augmented Reality
- Robotic Systems
- Fifth Generation (5G) Mobile Networks
On the other hand, the European Patent Office (EPO) presented a study on the patents that will have a significant impact on Industry 4.0. The main technologies that are driving the Fourth Industrial Revolution can be summarized as follows:
- Artificial intelligence (AI): AI is used to analyze large amounts of data and make intelligent decisions in real-time. This can help improve production efficiency, product quality, and predictive maintenance.
- Internet of Things (IoT): The IoT allows sensors and devices to be connected to the internet, which allows real-time data to be collected on the status of equipment and production processes.
- Cloud computing: Cloud computing provides a platform for storing and processing large amounts of data. This data can be used to train AI models, run simulations, and analyze historical data.
- Robotics: Robots are used to automate repetitive and dangerous tasks, which can improve safety and productivity.
- 3D printing: 3D printing allows the manufacture of personalized and complex parts quickly and efficiently.
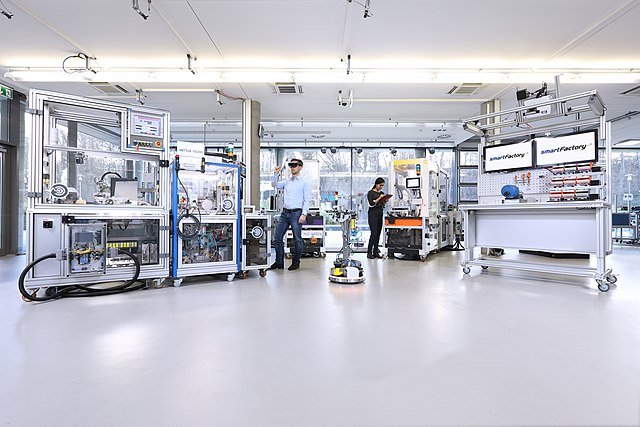
Principles for taking advantage of Industry 4.0
We must understand that the path to Industry 4.0 is a process of adopting information and communication technologies.
Gregolinska et al. (2022) describe seven fundamental principles for scaling a successful digital transformation that allows your company to get involved in the Fourth Industrial Revolution:
- Communicate well and often.
- Be specific: focus on real business needs and current performance challenges.
- Segment, select, and syndicate.
- Formalize value.
- Develop a three-to-five-year vision for the network.
- Design a digital manufacturing roadmap.
- Syndicate the vision and secure leadership buy-in.
Professional skills for the Fourth Industrial Revolution
The changes that are taking place with Industry 4.0 are forcing companies to look for professionals and technicians with skills related to digital technologies.
In this sense, as a professional you should think about strengthening your skills through training programs related to information and communication technologies, and database management.
In their study, Pejic-Bach et al. (2020) conclude that US or German companies immersed in smart manufacturing processes are demanding employees with two profiles:
- Employment profiles focused only on knowledge related to Industry 4.0: cyber-physical systems and the Internet of Things for robotic production; and intelligent production design and production control.
- Employment profiles focused on more general areas of knowledge that can be adapted to Industry 4.0: supply change management, customer satisfaction, and enterprise software.
Likewise, some digital education platforms offer courses with topics related to Industry 4.0:
- Coursera: Offers several courses on topics related to Industry 4.0, such as IoT, artificial intelligence, and supply chain management.
- edX: Platform that provides courses from recognized universities on technology and management topics related to Industry 4.0.
Examples of Industry 4.0
The digital technologies that drive the Fourth Industrial Revolution have been applied mainly in the manufacturing industry; however, it is also gaining importance in various economic and service sectors. Here are some examples of these applications:
Medicine
The COVID-19 pandemic scenario was the ideal setting for Industry 4.0 to show its full potential. Javaid et al., (2020) highlight that digital technologies provide an innovative method for the proper isolation of the COVID-infected patient, facilitating their care through telemedicine; it also allows for the acceleration of drug manufacturing, the treatment process, and care.
Another quite interesting example is the development of software based on artificial intelligence to identify skin cancer. For their part, Karatas et al., (2022) report that the healthcare sector is adopting the Fourth Industrial Revolution through the use of technologies such as the Internet of Health Things, cyber-physical medical systems, machine learning, and Big Data (BD).
Shipbuilding industry
Giallanza et al., (2020) studied, designed, and validated the preliminary implementation of Industry 4.0 in a prototype test bench for a high-power azimuthal thruster under full load conditions; they used Internet of Things sensors to collect and record data.
Agriculture
Bernhardt et al., (2021) indicate that the challenges for the implementation of Industry 4.0 in agriculture can be identified as process orientation, standardization, data communication, and knowledge transfer.
Likewise, smart crops are enabling the use of detailed digital information to guide decisions throughout the agricultural value chain; in this way, new technologies and solutions are being applied to provide alternatives that help in the collection and processing of information and, therefore, contribute to increasing agricultural productivity (Iaksch et al., 2021).
Food industry
Abdo et al., (2023) published a study in which they summarize the most relevant food technologies of Industry 4.0.
Industry 4.0 vs Industry 5.0?
As companies begin to adopt Industry 4.0, the European Commission is promoting the Fifth Industrial Revolution (Industry 5.0).
Xu et al., (2021) describe that Industry 4.0 is technology-driven while Industry 5.0 is value-driven; and that the Fifth Industrial Revolution recognizes the power of industry to achieve social goals beyond employment and growth, to become a resilient provider of prosperity.
Industry 5.0 complements the existing Industry 4.0 paradigm by highlighting research and innovation as drivers of a transition towards a sustainable, human-centered, and resilient industry (European Commission, 2021). In the article on Industry 5.0 you can find a more detailed comparison of the differences between both types of industries.
Challenges of Industry 4.0
While Industry 4.0 offers many benefits, some challenges need to be addressed, including:
- Cybersecurity: The increased use of interconnected devices and systems makes manufacturers more vulnerable to cyberattacks.
- Data privacy: The collection and use of large amounts of data raises concerns about data privacy and security.
- Workforce displacement: Automation and artificial intelligence could lead to job losses in some sectors of the manufacturing industry.
- Skills gap: The adoption of Industry 4.0 technologies will require workers to have new skills.
Conclusion
The Fourth Industrial Revolution represents a major shift in the way products and services are designed, manufactured, and marketed. It is characterized by the use of advanced technologies such as AI, IoT, cloud computing, and big data to connect machines, analyze data, and automate processes. In doing so, it is creating a more competitive environment in the industrial sector.
Industry 4.0 offers many benefits, including increased productivity, improved quality, reduced costs, increased flexibility, and new business models. However, some obstacles must be overcome, such as cybersecurity, data privacy, workforce displacement, and the skills gap.
Finally, we present many examples of the Fourth Industrial Revolution in sectors such as medicine, shipbuilding, and agriculture. In some way, these experiences are marking the path that the rest of the industries should follow.
References
Abdo Hassoun, Abderrahmane Aït-Kaddour, Adnan M. Abu-Mahfouz, Nikheel Bhojraj Rathod, Farah Bader, Francisco J. Barba, Alessandra Biancolillo, Janna Cropotova, Charis M. Galanakis, Anet Režek Jambrak, José M. Lorenzo, Ingrid Måge, Fatih Ozogul & Joe Regenstein (2023) The fourth industrial revolution in the food industry—Part I: Industry 4.0 technologies, Critical Reviews in Food Science and Nutrition, 63:23, 6547-6563, DOI: 10.1080/10408398.2022.2034735
Agrawal Mayank, Karel Eloot, Matteo Mancini, and Alpesh Patel. 2020. Industry 4.0: Reimagining manufacturing operations after COVID-19. McKinsey.
Bernhardt, Heinz, Mehmet Bozkurt, Reiner Brunsch, Eduardo Colangelo, Andreas Herrmann, Jan Horstmann, Martin Kraft, Johannes Marquering, Thilo Steckel, Heiko Tapken, Cornelia Weltzien, and Clemens Westerkamp. 2021. “Challenges for Agriculture through Industry 4.0” Agronomy 11, no. 10: 1935. https://doi.org/10.3390/agronomy11101935
Ching, N. T., Ghobakhloo, M., Iranmanesh, M., Maroufkhani, P., & Asadi, S. (2022). Industry 4.0 applications for sustainable manufacturing: A systematic literature review and a roadmap to sustainable development. Journal of Cleaner Production, 334, 130133.
European Commission, Directorate-General for Research and Innovation, Breque M, De Nul L, Petridis A. Industry 5.0 : towards a sustainable, human-centric and resilient European industry. Publications Office; 2021. Available from: doi/10.2777/308407
Giallanza, A., Aiello, G., Marannano, G. et al. Industry 4.0: smart test bench for shipbuilding industry. Int J Interact Des Manuf 14, 1525–1533 (2020). https://doi.org/10.1007/s12008-020-00739-9
Gonçalves Machado Carla, Mats Peter Winroth & Elias Hans Dener Ribeiro da Silva (2020) Sustainable manufacturing in Industry 4.0: an emerging research agenda, International Journal of Production Research, 58:5, 1462-1484, DOI: 10.1080/00207543.2019.1652777
Gregolinska Ewelina, Rehana Khanam, Frédéric Lefort, and Prashanth Parthasarathy. 2022. Capturing the true value of Industry 4.0. Mc Kinsey.
Guo Daqiang, Mingxing Li, Zhongyuan Lyu, Kai Kang, Wei Wu, Ray Y. Zhong, George Q. Huang. 2021. Synchroperation in industry 4.0 manufacturing. International Journal of Production Economics, Volume 238, 2021, 108171, ISSN 0925-5273, https://doi.org/10.1016/j.ijpe.2021.108171.
IBM. What is Industry 4.0?
Iaksch Jaqueline, Ederson Fernandes & Milton Borsato (2021) Digitalization and Big data in smart farming – a review, Journal of Management Analytics, 8:2, 333-349, DOI: 10.1080/23270012.2021.1897957
Karatas, M., Eriskin, L., Deveci, M., Pamucar, D., & Garg, H. (2022). Big Data for Healthcare Industry 4.0: Applications, challenges and future perspectives. Expert Systems with Applications, 200, 116912.
Marr Bernard. 2018. What is Industry 4.0? Here’s A Super Easy Explanation For Anyone. Forbes.
Masood Tariq, Paul Sonntag. 2020. Industry 4.0: Adoption challenges and benefits for SMEs. Computers in Industry, Volume 121, 2020, 103261, ISSN 0166-3615,
https://doi.org/10.1016/j.compind.2020.103261
Meindl Benjamin, Néstor Fabián Ayala, Joana Mendonça, Alejandro G. Frank. 2021. The four smarts of Industry 4.0: Evolution of ten years of research and future perspectives. Technological Forecasting and Social Change, Volume 168, 2021, 120784, ISSN 0040-1625, https://doi.org/10.1016/j.techfore.2021.120784.
Oláh, Judit, Nemer Aburumman, József Popp, Muhammad Asif Khan, Hossam Haddad, and Nicodemus Kitukutha. 2020. “Impact of Industry 4.0 on Environmental Sustainability” Sustainability 12, no. 11: 4674. https://doi.org/10.3390/su12114674
Pejic-Bach Mirjana, Tine Bertoncel, Maja Meško, Živko Krstic. 2020. Text mining of industry 4.0 job advertisements. International Journal of Information Management, Volume 50, 2020, Pages 416-431, ISSN 0268-4012, https://doi.org/10.1016/j.ijinfomgt.2019.07.014.
Sigov, A., Ratkin, L., Ivanov, L.A. et al. Emerging Enabling Technologies for Industry 4.0 and Beyond. Inf Syst Front (2022). https://doi.org/10.1007/s10796-021-10213-w
Slusarczyk, B. Industry 4.0: Are we ready? Pol. J. Manag. Stud. 2018, 17, 232–248.
Xu Xun, Yuqian Lu, Birgit Vogel-Heuser, Lihui Wang. 2021. Industry 4.0 and Industry 5.0—Inception, conception and perception. Journal of Manufacturing Systems, Volume 61, 2021, Pages 530-535, ISSN 0278-6125, https://doi.org/10.1016/j.jmsy.2021.10.006.

Editor and founder of “Innovar o Morir” (‘Innovate or Die’). Milthon holds a Master’s degree in Science and Innovation Management from the Polytechnic University of Valencia, with postgraduate diplomas in Business Innovation (UPV) and Market-Oriented Innovation Management (UPCH-Universitat Leipzig). He has practical experience in innovation management, having led the Fisheries Innovation Unit of the National Program for Innovation in Fisheries and Aquaculture (PNIPA) and worked as a consultant on open innovation diagnostics and technology watch. He firmly believes in the power of innovation and creativity as drivers of change and development.