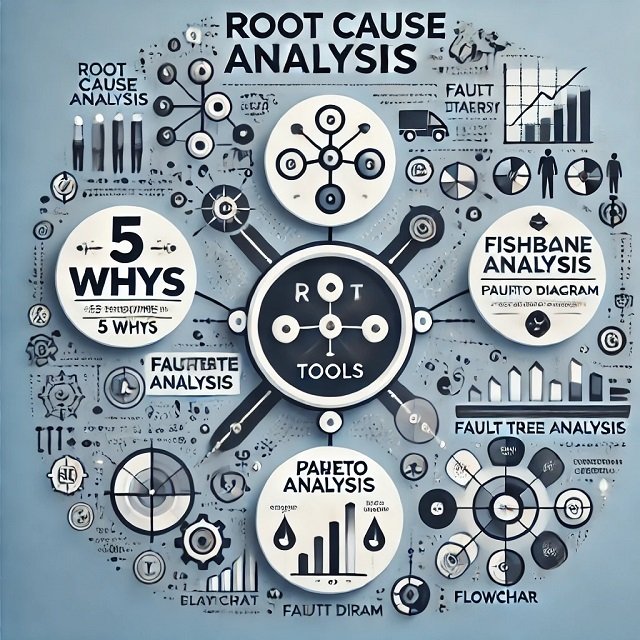
Root Cause Analysis (RCA) is a fundamental methodology in quality management, problem-solving, and continuous improvement. It is a valuable management tool that can be easily learned by managers and frontline staff (Peerally et al., 2017), healthcare personnel (Singh et al., 2024), audit firms, regulators, policymakers (Groot, 2021), among other professionals and technicians, to solve problems.
The Root Cause Analysis methodology provides the opportunity to learn from past adverse events and prevent them from happening again in the future (Groot, 2021). This article will guide you through the concepts, tools, and practical applications of RCA, including examples in industries such as healthcare, manufacturing, and project management. You will learn what it is, how to implement it, and why it is essential for organizational success.
What is Root Cause Analysis?
Root Cause Analysis (RCA) is a systematic approach to identifying the primary cause of a problem and eliminating it to prevent recurrence. According to Oliveira et al., (2023), RCA is the process of finding the true cause of a problem; in the same vein, Shaqdan et al., (2014) highlight that RCA is a retrospective approach used to determine the “root cause” of a problem that has already occurred.
Unlike methods that only address symptoms, Root Cause Analysis delves into the “why” behind a failure, ensuring effective and sustainable solutions.
What is the goal of Root Cause Analysis?
The primary goal of RCA is to prevent the recurrence of the problem. This is achieved by identifying and eliminating the underlying causes. This approach ensures that organizations not only address immediate problems but also implement strong preventive measures.
Doggett (2005) emphasizes that RCA tools should also promote focus, stimulate debate, be legible when completed, and have mechanisms to assess the integrity of the group’s findings.
Benefits of Using Root Cause Analysis
Pargaonkar (2023) describes that the main benefits of employing root cause analysis are:
- Sustainable solutions: Addressing root causes ensures that defects are not only temporarily solved but also prevented from reappearing in the future.
- Process improvement: Discovering process deficiencies through root cause analysis allows for refining them, leading to stronger development practices.
- Continuous learning: The insights gained from root cause analysis contribute to organizational learning, enabling teams to make informed decisions and avoid repeating mistakes.
- Risk mitigation: By addressing the core problems, root cause analysis minimizes the risk of similar defects causing disruptions in future projects.
Steps to Perform a Root Cause Analysis
- Define the problem: Document what happened, when, where, and the impact it had.
- Collect data: Gather objective evidence such as records, testimonies, and measurements.
- Identify possible causes: Use tools like fishbone diagrams.
- Determine the root cause: Conduct deeper analysis, such as the 5 Whys.
- Develop solutions: Design corrective actions that address the real causes.
- Implement and monitor: Apply the solutions and evaluate their long-term effectiveness.
Key Tools for Root Cause Analysis
Among the most effective tools for Root Cause Analysis (RCA) are:
5 Whys (5 Why Analysis)
The 5 Whys method is a simple yet powerful tool used in Root Cause Analysis (RCA). This technique is based on the premise that behind every obvious problem, there is a chain of underlying causes, and by repeatedly asking “Why?”, the root cause can be identified. Although exactly five questions are not always necessary, this number is typically enough to get to the core of the problem.
Below is a detailed example of the 5 Whys process in a practical case:
- Why did the defect occur? Answer: Because the material used in production was inadequate. Analysis: This is the initial symptom. To understand why the material was inadequate, further inquiry is needed.
- Why was inadequate material used? Answer: Because the supplier was not properly verified before placing the order. Analysis: This points to a failure in the supplier selection or evaluation process.
- Why wasn’t the supplier verified? Answer: Because there is no standard procedure for supplier verification. Analysis: This identifies a systemic issue: the lack of a formal protocol.
- Why is there no standard procedure for supplier verification? Answer: Because the company has not prioritized creating formal policies to ensure supplier quality. Analysis: This reflects a management or strategic focus problem.
- Why has the company not prioritized creating these policies? Answer: Because in the past, it was not considered a critical need due to excessive trust in recurring suppliers. Analysis: This leads to the root cause: the lack of foresight and risk management in the supply chain.
Fishbone Diagram (Cause and Effect Diagram)
Also known as the Ishikawa diagram, it categorizes and visualizes the possible causes of a problem. Srinivasaragavan et al., (2024) suggests that the Fishbone Diagram should be written on the right side of the board. An arrow should be drawn ending in the problem at hand, with six main categories that led to the problem as major branches. Each main category should list all possible causes underneath it.
Statistical Analysis Methods
These include histograms and control charts, useful for problems related to variability.
Process Mapping
Identifies failures in specific steps within a workflow.
Templates and Forms for Root Cause Analysis
The use of structured templates facilitates the implementation of Root Cause Analysis. Some common options include:
- Excel Templates: These allow for organized recording of problems, corrective actions, and results. An example of using Excel is provided in Appendix 01.
- Standard Forms: Simplify data collection and highlight critical areas.
Examples of Root Cause Analysis Use
Example in Healthcare
Root Cause Analysis (RCA) is a framework used in healthcare to determine systemic causes and prevent the recurrence of adverse events (Percarpio et al., 2008). According to Singh et al. (2024), RCA provides a method for evaluating “medical errors” so that a system-based intervention can be implemented instead of blaming individual doctors.
In a hospital setting, RCA may reveal that falls are due to insufficient lighting or the absence of handrails, proposing specific improvements. Shaqdan et al. (2014) reports that RCA and Failure Mode and Effect Analysis (FMEA) are used to maintain high standards in healthcare quality and incorporate modifications that save time and costs to favorably affect the patient care environment.
Example in Project Management
A delay in delivery could stem from a lack of resources or inadequate planning. RCA would help identify and correct these deficiencies.
Tilocca et al., (2024) used the Fishbone Diagram and the traditional logical tree (the 5 Whys method) to analyze the failure in the gas microturbine market and concluded that the proposed methodology proved capable of solving complex business and technology problems in a more scientific, holistic, and objective manner compared to common industry practices.
Join the Community
Get the best ideas, analysis, and trends on innovation delivered straight to your inbox. No spam, just value!
Example in Education
Francis (2021) reported using the 5 Whys method to help students deepen their analysis (causes and effects) of a social problem in U.S. institutions; he believes that using Root Cause Analysis by university students becomes a tool to develop critical thinking and collaboration skills.
Specific Applications of RCA
Root Cause Analysis in Six Sigma
Root Cause Analysis (RCA) is a key technique in Six Sigma used to identify the underlying causes of a problem and ensure that they are permanently solved. In the context of Six Sigma, RCA is primarily integrated during the Analyze phase of the DMAIC cycle (Define, Measure, Analyze, Improve, Control).
Steps in Using RCA in Six Sigma
- Problem Definition: Clearly identify the problem in measurable terms. Example: “The defect percentage on the assembly line has increased to 8%.”
- Data Collection: Use Six Sigma tools such as check sheets, histograms, and control charts to understand the magnitude and context of the problem. Example: Analyze defects by shift, machine, or batch.
- Identifying Potential Causes: Use tools such as:
- Ishikawa Diagram (Cause-Effect): To group possible causes into categories such as methods, materials, labor, machines, environment, and measurement.
- The 5 Whys: Ask “Why?” repeatedly until the root cause is identified.
- Data Analysis: Verify possible causes using quantitative data. Example: Use Pareto analysis to identify the main causes of defects.
- Root Cause Validation: Confirm that the identified cause has a direct correlation with the problem. This can be done with controlled tests or experiments.
- Solution Implementation: Design and implement solutions to eliminate the root cause. Example: If the cause is a poorly defined procedure, redesign and implement a new standard operating procedure.
- Monitoring and Control: Use control charts to monitor the process after implementing the solution and ensure that the problem does not recur.
RCA in Lean Management
In Lean Management, Root Cause Analysis (RCA) is a fundamental tool for identifying and eliminating the underlying causes of problems that generate waste or inefficiencies in processes. This is essential for fulfilling the key principle of Lean: continuously improving value streams and eliminating activities that do not add value.
Steps in Using RCA in Lean
- Problem Definition: Clearly specify the problem being addressed, preferably from the customer’s perspective. Example: “Order delivery time has increased by 3 days in the last month.”
- Process Mapping (Value Stream Mapping): Analyze the workflow and the points where the problem is generated. Identify steps that do not add value and analyze how they impact the problem.
- Identification of Potential Causes: Use visual tools such as:
- Ishikawa Diagram (Cause-Effect): To identify potential categories of causes.
- The 5 Whys: To delve deeper into analyzing each cause.
- Root Cause Validation: Confirm with data and direct observation at the work site (Gemba) that the identified root cause is truly related to the problem. Example: If the potential cause is the lack of materials, validate by reviewing inventory history.
- Implementation of Countermeasures: Design actions that eliminate the root cause and ensure the problem does not recur. Example: Implement a just-in-time replenishment system to prevent material shortages.
- Monitoring and Continuous Improvement: Monitor the process to ensure that the countermeasures are effective. Use key performance indicators (KPIs) to measure the impact of the improvements.
RCA vs FMEA
While both are related to risk management, RCA analyzes problems that have already occurred, whereas FMEA (Failure Mode and Effect Analysis) is preventive, identifying potential risks. Shaqdan et al. (2014) reports that Root Cause Analysis and Failure Mode and Effect Analysis are used to prevent errors or recurring issues to create a safer workplace.
Table 01: Comparative Analysis: Root Cause Analysis (RCA) vs. Failure Mode and Effect Analysis (FMEA)
Aspect | Root Cause Analysis (RCA) | Failure Mode and Effect Analysis (FMEA) |
---|---|---|
Purpose | Identify and eliminate the root cause of a problem that has already occurred. | Identify potential failures in a system or process before they occur and prioritize their mitigation. |
Timing of Application | Reactive: Applied after the problem has occurred. | Proactive: Applied during planning or design of processes or systems to prevent problems. |
Approach | – Focuses on a specific problem. | – Examines multiple potential failures in a system. |
– Seeks the root cause(s) that led to the event. | – Analyzes failure modes, effects, and causes for each component or process. | |
Key Tools | – Ishikawa Diagram (Cause-Effect). | – Structured FMEA table. |
– The 5 Whys. | – Severity, occurrence, and detection scales (RPN: Risk Priority Number). | |
Expected Outcomes | – Elimination of the root cause and prevention of recurrence. | – Prioritized list of potential failures with action plans to mitigate or reduce their impact and likelihood. |
Common Application | – Resolving recurring issues in production, quality, or services. | – Designing new processes or products. |
– Evaluating existing systems to identify vulnerabilities before implementation. | ||
Level of Detail | More detailed analysis of a single problem, drilling down to the root cause. | Broader, covering multiple components, processes, or systems to identify a variety of potential failures. |
Use of Data | Requires historical data and evidence to validate the root cause. | Based on historical data, expert experience, and forecasting of system and process behavior. |
Team Requirements | Cross-functional teams to investigate the problem at the site where it occurred. | Multidisciplinary teams with technical knowledge of the system or process being analyzed. |
Execution Time | Can be quick or take time, depending on the complexity of the problem. | Can take significant time due to the exhaustive analysis of each potential failure mode. |
Scalability | Applied to specific and concrete problems. | Can be applied to complex systems, processes, or products with multiple components. |
Organizational Culture | Encourages a reactive mindset but with continuous improvement to solve problems. | Promotes a proactive culture of prevention and risk management. |
Benefits of Using Root Cause Analysis Software
Digital tools enhance RCA by automating tasks such as:
- Documentation of findings.
- Tracking of corrective actions.
- Generation of detailed reports.
For example, Ma et al., (2021) proposes a conceptual framework for a root cause analysis system based on big data that includes three modules: Problem Identification, Root Cause Identification, and Permanent Corrective Action. Meanwhile, Papageorgiou et al., (2022) states that many artificial intelligence technologies have already been successfully incorporated into the root cause analysis framework for defect-free manufacturing.
Wang et al., (2024) designed an enhanced root cause analysis method with knowledge graphs (KGroot) for efficient and effective diagnosis of recurring failures in complex microservice environments.
Conclusion
Root Cause Analysis (RCA) is an essential methodology for addressing complex problems and preventing their recurrence. By applying tools such as the 5 Whys, fishbone diagrams, and advanced techniques, organizations can transform their processes into resilient and proactive models. Implementing RCA not only solves current problems but also establishes a solid foundation for continuous improvement and long-term success.
References
Doggett, A. M. (2005). Root Cause Analysis: A Framework for Tool Selection. Quality Management Journal, 12(4), 34–45. https://doi.org/10.1080/10686967.2005.11919269
Francis, D. M. (2021). Using Root Cause Analysis to Help Students Examine Social Problems. Teaching Journalism & Mass Communication, 11(1), 61-64.
Groot, W. (2021). Root cause analysis–what do we know?. Maandblad voor accountancy en bedrijfseconomie, 95(1/2), 87-93.
Ma, Q., Li, H., & Thorstenson, A. (2021). A big data-driven root cause analysis system: Application of Machine Learning in quality problem solving. Computers & Industrial Engineering, 160, 107580. https://doi.org/10.1016/j.cie.2021.107580
Oliveira, E., Miguéis, V.L. & Borges, J.L. Automatic root cause analysis in manufacturing: an overview & conceptualization. J Intell Manuf 34, 2061–2078 (2023). https://doi.org/10.1007/s10845-022-01914-3
Pargaonkar, S. (2023). Defect management and root cause analysis: Pillars of excellence in software quality engineering. International Journal of Science and Research (IJSR), 12(9), 53-55.
Papageorgiou, K., Theodosiou, T., Rapti, A., Papageorgiou, E. I., Dimitriou, N., Tzovaras, D., & Margetis, G. (2022). A systematic review on machine learning methods for root cause analysis towards zero-defect manufacturing. Frontiers in Manufacturing Technology, 2, 972712. https://doi.org/10.3389/fmtec.2022.972712
Percarpio, K. B., Watts, B. V., & Weeks, W. B. (2008). The Effectiveness of Root Cause Analysis: What Does the Literature Tell Us? The Joint Commission Journal on Quality and Patient Safety, 34(7), 391-398. https://doi.org/10.1016/S1553-7250(08)34049-5
Peerally, M. F., Carr, S., Waring, J., & Dixon-Woods, M. (2017). The problem with root cause analysis. BMJ quality & safety, 26(5), 417-422.
Shaqdan, K., Aran, S., Daftari Besheli, L., & Abujudeh, H. (2014). Root-Cause Analysis and Health Failure Mode and Effect Analysis: Two Leading Techniques in Health Care Quality Assessment. Journal of the American College of Radiology, 11(6), 572-579. https://doi.org/10.1016/j.jacr.2013.10.024
Singh, G., Patel, R. H., Vaqar, S., & Boster, J. (2024). Root cause analysis and medical error prevention. In StatPearls [internet]. StatPearls Publishing.
Srinivasaragavan, D., Ramalingam, K., & Ramani, P. (2024). Root Cause Analysis: Unraveling Common Laboratory Challenges. Cureus, 16(2), e53393. https://doi.org/10.7759/cureus.53393
Tilocca, G., Sánchez, D., & Torres-García, M. (2024). Applying the root cause analysis methodology to study the lack of market success of micro gas turbine systems. Applied Energy, 360, 122717. https://doi.org/10.1016/j.apenergy.2024.122717
Wang, T., Qi, G., & Wu, T. (2024). KGroot: A knowledge graph-enhanced method for root cause analysis. Expert Systems With Applications, 255, 124679. https://doi.org/10.1016/j.eswa.2024.124679
Annex 01: Increase in Waiting Time in a Hospital’s Emergency Room
Problem
Patients are experiencing waiting times exceeding 4 hours in the emergency department.
Steps to Create the Analysis in Excel
Identification of the Main Problem:
In an initial cell, write the problem: “Increase in waiting time in emergencies.”
List Possible Causes:
Create a table in Excel with columns such as:
- Cause
- Subcause
- Evidence
- Evaluation (Likely / Unlikely)
Example of possible causes:
- Patient overload
- Lack of staff
- Inefficient processes
- Failures in the triage system
Data Collection:
Record historical data on waiting times, number of patients, staff availability, etc.
Example of columns:
- Date
- Number of patients attended
- Average waiting time (minutes)
- Available staff
- Observations
Cause Analysis:
Use Excel formulas to identify patterns:
- =AVERAGE(A2:A30) to calculate the average waiting time.
- =STDEV.P(A2:A30) to analyze data variability.
Use pivot tables to filter by days, shifts, or work teams.
Action Plan:
Add a column for corrective actions:
- Cause: Lack of staff.
- Action: Hire additional staff for critical shifts.
Graphical Representation:
Create line or bar charts to show:
- Waiting times by day.
- Relationship between the number of patients and available staff.
Excel Table Design
Problem | Cause | Subcause | Evidence | Evaluation | Corrective Action |
---|---|---|---|---|---|
High waiting times | Patient overload | High influx during peaks | Patient records > 100 | Likely | Implement scheduled appointments |
Lack of staff | Unfilled vacancies | Shifts with < 50% capacity | Likely | Hire additional staff | |
Inefficient processes | Slow triage | Triage time > 10 minutes | Unlikely | N/A |

Editor and founder of “Innovar o Morir” (‘Innovate or Die’). Milthon holds a Master’s degree in Science and Innovation Management from the Polytechnic University of Valencia, with postgraduate diplomas in Business Innovation (UPV) and Market-Oriented Innovation Management (UPCH-Universitat Leipzig). He has practical experience in innovation management, having led the Fisheries Innovation Unit of the National Program for Innovation in Fisheries and Aquaculture (PNIPA) and worked as a consultant on open innovation diagnostics and technology watch. He firmly believes in the power of innovation and creativity as drivers of change and development.