
Industries are under tremendous pressure to innovate and produce high-quality products at a rapid rate due to market competitiveness (Samah et al., 2023). In this context, entrepreneurs are actively seeking technologies that allow them to maintain their competitive edge.
Injection molding is a manufacturing process used to create three-dimensional objects from melted plastic, metals, ceramics, or other materials. While the process is conceptually straightforward, its practical implementation can be complex, heavily relying on the quality and efficiency of molding tools (Rocha et al., 2022).
Injection molding has experienced rapid growth, driven by the development of new applications in the automotive/transportation, electronics, medical, and packaging industries (Fernandes et al., 2018). Today, it stands as one of the most popular techniques for mass production of plastic (Ageyeva et al., 2019) and other materials.
Technological advancements, process flexibility, sustainability, and the increasing demand for customized solutions contribute to the growing popularity of injection molding as a manufacturing method (Czepiel et al., 2023).
Injection molds are primarily used as semi-finished or finished parts that can be employed to produce final products (Jung et al., 2021). Unlike 3D printing, which is ideal for intricate geometries, injection molding is well-suited for mass production (Boros et al., 2019) due to its higher production rate.
This guide provides an overview of injection molding technology, covering basic principles, the process, and the materials commonly used.
What Is Injection Molding?
Injection molding is a process that heats and melts polymers, metals, and other materials before injecting them into a mold cavity. The material cools and hardens in the mold, and the mold is then opened to release the finished product.
Injection molding is a suitable method for the mass production of products with complex shapes and is primarily used in the plastic industry. Fernandes et al., (2018) emphasize that one of the main goals of injection molding is to improve the quality of molded parts at a lower cost. Additionally, this technology is employed to produce smaller parts (Senthil, 2022) that are often challenging to manufacture using other production methods.
According to Sina (2015), the principle of injection molding is straightforward: plastic material is heated until it becomes a viscous molten mass; it is then introduced into a closed mold defining the shape of the article to be produced; the material is cooled until it solidifies again, and then the mold is opened to extract the finished piece.
History of Injection Molding
Injection molding was first developed in the 19th century when a relatively simple machine was created to mold buttons, combs, and other small items (Czepiel et al., 2023), quickly becoming a popular manufacturing process.
The early injection molding machines were relatively simple but have evolved significantly over the years. Modern injection molding machines are highly automated and can produce complex products with high precision.
The injection molding industry has evolved over decades and has become the most common method for manufacturing plastic parts (Liau et al., 2018); however, its application has expanded across many industries.
Injection Molding Machine
An injection molding machine is the equipment used to perform the injection molding process. There are different types of injection molding machines based on how the drives are powered: hydraulic, hybrid, and fully electric (Elduque et al., 2015).
The main components of an injection molding machine are:
- Mold: The mold is the cavity used to shape the finished product.
- Barrel: The barrel is a heated chamber containing melted plastic.
- Screw: The screw is used to melt and transport the plastic through the cylinder.
- Nozzle: The nozzle is used to inject the melted plastic into the mold cavity.
- Clamping Unit: The clamping unit keeps the mold closed during the injection and cooling processes.
Injection Molding Process
Injection molding is a manufacturing process used to create three-dimensional objects from melted plastic. The process is simple in principle but can be complex in practice.
Injection molding is a molding technology that melts the material with the help of a screw and an external heating device and then injects it into a mold to form the corresponding product as the mold cools (Fu et al., 2020). A common concern when employing this technology is the differences between the designed shape and the actual parts, all associated with shrinkage and warping phenomena (Manoraj et al., 2017).
The basic steps of injection molding are as follows:
- Melting: The first step is to melt the thermoplastic material. This can be done using a heated cylinder and a screw. The screw rotates, pushes the material through the cylinder, and melts it as it advances.
- Injection: Next, the melted material is injected into the mold cavity. The pressure and speed of the injection process are important factors affecting the quality of the finished product. The pressure must be high enough to force the material into all details of the mold cavity but not so high as to damage the mold. The injection speed must be fast enough to prevent the material from cooling before filling the mold cavity but not so fast as to create turbulence that can cause defects in the finished product.
- Cooling: The material cools and hardens in the mold. The cooling time depends on the type of plastic used. The cooling time should be long enough for the material to harden completely but not so long that the piece deforms or shrinks.
- Ejection: The mold is then opened to release the finished product. The ejection process must be gentle enough not to damage the piece but not so gentle that the piece sticks to the mold.
Regardless of the molding process you use, it is important to note that molding conditions (melting temperature, mold temperature, filling time, packing time, and packing pressure) also impact the productivity, cycle time, and energy consumption of the molding process. Molding conditions are closely related to other factors such as materials, part design, and tools, which determine the quality of plastic products (Dang, 2014).
Join the Community
Get the best ideas, analysis, and trends on innovation delivered straight to your inbox. No spam, just value!
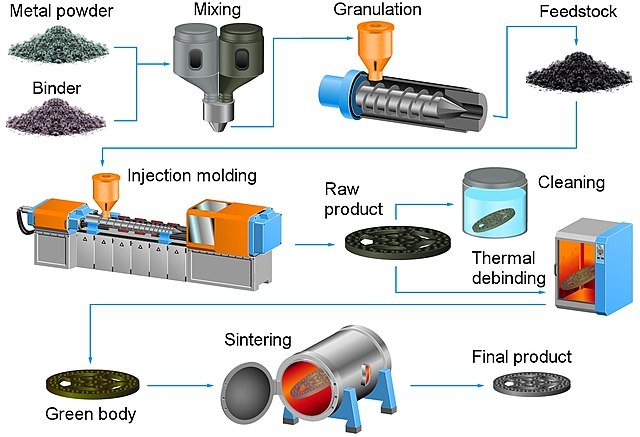
In recent years, there has been a drive towards smart injection molding, referring to a production process that employs artificial intelligence technology to develop an online optimization system (Ageyeva et al., 2019) and can be used in the context of Industry 4.0.
Materials for Injection Molding
A wide variety of thermoplastic materials can be used in injection molding. Some widely used materials include polyvinyl chloride (PVC), nylon, polyamide, polyester, acrylic, glass, and elastomers. Additionally, almost all metals can be molded using the metal injection molding process (Senthil et al., 2022).
Here’s a brief description of the main materials used in injection molding, based on the study by Czepiel et al., (2023), and information from companies providing injection molding services:
- Polyethylene: Polyethylene is a versatile material used in a wide range of applications. Derived from the polymerization of ethylene, it is characterized by its flexibility, ductility, heat resistance, electrical resistance, chemical resistance, and degradation resistance.
- Polypropylene: Polypropylene is a strong and durable material often used in industrial and automotive applications. Its low viscosity in a molten state allows for a smooth and fluid consistency. It is easily moldable and allows for the molding of products of any shape. It is resistant to erosion, oxidation, and chemical spills.
- Polystyrene: Polystyrene is a lightweight and economical material often used in packaging and consumer products. It is one of the most widely used polymers in the world and can be found in various forms, with expanded polystyrene (EPS), also known as Styrofoam, being a common type.
- Acrylonitrile Butadiene Styrene (ABS): ABS is a strong and impact-resistant material often used in automotive and industrial applications. This copolymer consists of 15 to 35% acrylonitrile, 5 to 30% butadiene, and 40 to 60% styrene.
- Polyvinyl Chloride (PVC): PVC is one of the most popular and widely used synthetic polymers. Due to its corrosion resistance, durability, and ease of processing, PVC is the material of choice for creating sewer systems, water systems, pipes, windows, doors, and extensively in the packaging industry. It is also used in the furniture, medical, and automotive industries.
- Nylon: Nylon is a strong and durable material often used in mechanical and electrical applications.
- Metals: Virtually all metals, except aluminum and magnesium.

Injection Molding Applications
Injection molding is a versatile process that can be used to produce a wide variety of products. Jung et al. (2021) report that injection molds are frequently used in the manufacturing of plastic parts, and these parts find applications in various businesses such as automotive manufacturing, footwear, and electronics.
Some of the most common applications of injection molding include:
- Consumer Products: Injection molding is used to produce a wide variety of consumer products such as toys, appliances, and packaging.
- Automotive: Injection molding is employed to manufacture various automotive components like bumpers, dashboards, and steering wheels.
- Medical Devices: Injection molding is used to produce a broad range of medical devices such as syringes, implants, and surgical instruments.
Plastic Injection Molding Examples
As previously explained, plastic injection molding is the most widely employed technology. However, it’s essential to note that this technology is being used across different industries with various materials.
Here are specific examples of products manufactured through plastic injection molding:
- Toys: Plastic toys, including action figures, dolls, and building blocks, are commonly produced using plastic injection molding.
- Appliances: Plastic appliances like refrigerators, washing machines, and dishwashers are also commonly manufactured through plastic injection molding.
- Packaging: Plastic packaging, such as bottles, containers, and trays, represents another common product produced through plastic injection molding.
- Automotive Parts: Plastic automotive parts like bumpers, dashboards, and steering wheels are frequently manufactured through plastic injection molding.
- Medical Devices: Plastic medical devices, including syringes, implants, and surgical instruments, are also commonly produced using plastic injection molding.
Plastic injection molding is a versatile process that can be used to produce a wide range of products. It is an efficient process that can produce high-quality products at a relatively low cost; this characteristic has made it a very popular technology for use in the production of plastic-based products.
Advantages of Injection Molding
Research by Kazmer et al. (2023) emphasizes that injection molding will remain more economical and sustainable for high-volume applications until the high energy consumption of additive manufacturing is reduced. Tosello et al. (2019) report that injection molding for polymer tool insert manufacturing is economically advantageous, resulting in an 80 to 90% reduction in production costs compared to a conventional tooling process based on machining.
According to Czepiel et al. (2023), injection molding plays a crucial role in sustainable development by reducing raw material consumption, minimizing waste, and promoting recycling.
Injection molding offers several advantages over other manufacturing processes, including:
- High Precision: Injection molding can produce complex products with high precision.
- High Production Rates: Injection molding can produce large quantities of products quickly and efficiently.
- Wide Range of Applications: Injection molding can be used to produce a wide variety of products.
Disadvantages of Injection Molding
Like any technology, injection molding also has some disadvantages that act as a barrier to broader adoption across all industries.
The main disadvantages of injection molding can be summarized as follows:
- High Initial Costs: Injection molding machines can be expensive to purchase and maintain.
- Complex Process: Injection molding is a complex process that requires skilled operators.
- Waste: Injection molding can generate a significant amount of waste material. In recent years, research has been conducted to determine waste generation and energy demand.
Conclusion
Injection molding is a versatile and efficient manufacturing process that can be used to produce a wide variety of products. By understanding the basic principles of injection molding, you can make informed decisions about when and how to use this process.
Currently, injection molding has promising growth prospects in various industries as automation and robotization of injection molding processes become more advanced (Czepiel et al., 2023). Similarly, Boros et al. (2019) report the possibilities of combining the two most important polymer processing technologies: injection molding and 3D printing, thereby expanding the fields of application for these technologies.
Although it is a technology created more than a century ago, Injection Molding has been continuously updated due to technological advancements and the availability of new materials. With these advances, this technology is poised to play a significant role in Industry 4.0, primarily as a method of smart manufacturing.
References
Ageyeva, Tatyana, Szabolcs Horváth, and József Gábor Kovács. 2019. “In-Mold Sensors for Injection Molding: On the Way to Industry 4.0” Sensors 19, no. 16: 3551. https://doi.org/10.3390/s19163551
Boros, R., Rajamani, P. K., & Kovacs, J. G. (2019). Combination of 3D printing and injection molding: Overmolding and overprinting. Express Polymer Letters, 13(10).
Czepiel, Mateusz, Magdalena Bankosz, and Agnieszka Sobczak-Kupiec. 2023. “Advanced Injection Molding Methods: Review” Materials 16, no. 17: 5802. https://doi.org/10.3390/ma16175802
Dang, X. P. (2014). General frameworks for optimization of plastic injection molding process parameters. Simulation Modelling Practice and Theory, 41, 15-27.
Elduque, A., Elduque, D., Javierre, C., Fernández, Á., & Santolaria, J. (2015). Environmental impact analysis of the injection molding process: analysis of the processing of high-density polyethylene parts. Journal of Cleaner Production, 108, 80-89.
Fernandes, C., Pontes, A.J., Viana, J.C. and Gaspar-Cunha, A. (2018), Modeling and Optimization of the Injection-Molding Process: A Review. Adv. Polym. Technol., 37: 429-449. https://doi.org/10.1002/adv.21683
Fu, H., Xu, H., Liu, Y., Yang, Z., Kormakov, S., Wu, D., & Sun, J. (2020). Overview of injection molding technology for processing polymers and their composites. ES Materials & Manufacturing, 8(4), 3-23.
Jung, Hail, Jinsu Jeon, Dahui Choi, and Jung-Ywn Park. 2021. “Application of Machine Learning Techniques in Injection Molding Quality Prediction: Implications on Sustainable Manufacturing Industry” Sustainability 13, no. 8: 4120. https://doi.org/10.3390/su13084120
Kazmer, D., Peterson, A. M., Masato, D., Colon, A. R., & Krantz, J. (2023). Strategic cost and sustainability analyses of injection molding and material extrusion additive manufacturing. Polymer Engineering & Science, 63(3), 943-958.
Liau, Y., Lee, H., & Ryu, K. (2018, March). Digital Twin concept for smart injection molding. In IOP Conference Series: Materials Science and Engineering (Vol. 324, p. 012077). IOP Publishing.
Manoraj Mohan, M.N.M. Ansari & Robert A. Shanks (2017) Review on the Effects of Process Parameters on Strength, Shrinkage, and Warpage of Injection Molding Plastic Component, Polymer-Plastics Technology and Engineering, 56:1, 1-12, DOI: 10.1080/03602559.2015.1132466
Rocha, Sofia B., Tatiana Zhiltsova, Victor Neto, and Mónica S. A. Oliveira. 2022. “Optimization to Assist Design and Analysis of Temperature Control Strategies for Injection Molding—A Review” Materials 15, no. 12: 4048. https://doi.org/10.3390/ma15124048
Samah, S., Borse, D. Y., & Sulakhe, V. N. 2023. Improved Productivity and Efficient Manufacturing Using Injection Molding and 3D Printing: A Review.
Senthil Kumaran Selvaraj, Aditya Raj, R. Rishikesh Mahadevan, Utkarsh Chadha, Velmurugan Paramasivam, “A Review on Machine Learning Models in Injection Molding Machines“, Advances in Materials Science and Engineering, vol. 2022, Article ID 1949061, 28 pages, 2022. https://doi.org/10.1155/2022/1949061
Sina Ebnesajjad. 2015. 10 – Injection Molding, Editor(s): Sina Ebnesajjad, Fluoroplastics (Second Edition), William Andrew Publishing, 2015, Pages 236-281, ISBN 9781455731978, https://doi.org/10.1016/B978-1-4557-3197-8.00010-9.
Tosello, G., Charalambis, A., Kerbache, L., Mischkot, M., Pedersen, D. B., Calaon, M., & Hansen, H. N. (2019). Value chain and production cost optimization by integrating additive manufacturing in injection molding process chain. The International Journal of Advanced Manufacturing Technology, 100, 783-795.

Editor and founder of “Innovar o Morir” (‘Innovate or Die’). Milthon holds a Master’s degree in Science and Innovation Management from the Polytechnic University of Valencia, with postgraduate diplomas in Business Innovation (UPV) and Market-Oriented Innovation Management (UPCH-Universitat Leipzig). He has practical experience in innovation management, having led the Fisheries Innovation Unit of the National Program for Innovation in Fisheries and Aquaculture (PNIPA) and worked as a consultant on open innovation diagnostics and technology watch. He firmly believes in the power of innovation and creativity as drivers of change and development.